Many Polysix’ will be hit by a sudden photocoupler death somewhen.
There are many “facts” around on the internet describing how do determine whether it has failed and how to substitute the unavailable IC.
Fact 1: it is not true that you can check the photocoupler by measuring the voltage drop on the 4k7 resistor inseries with the LED or even the voltage drop across the LED.
LEDs do fail without exhibiting any dramatic change in electrical parameters. You will find LEDs which drop 1.6 volts @ 20 millamps and emitting no light!
(That – and some scientific applications – is why some applications still require incandescent lamps, and that’s why I’ve designed a controller for a 1960s filament winding machine in 2010!)
In this special case, the LDR saturated at 5.4 megohms with full LED current, so either the LED has become dark or the LDR insensitive.
The only way to check the photocoupler is to remove it from the circuit and measure the LDR resistance versus the LED current and compare it to a known working part (see diagram below)
Some background: the photcoupler is used in a feedback loop to stabilize the expo converter which makes up the V/Hz scale for the VCOs from the octave/V control voltage.
To use only one expo, Korg has used multiplexers to feed the 6 VCO CVs to the expo, followed by a calibration voltage and then the CV for standard pitch (only for the new production voice board).
The two latter outputs are routed to two independent controllers; the last one introduces an offset to the expo input to shift the standard pitch to its desired value, while the converted calibration voltage drives a current through the photocoupler’s LED, while its LDR is placed where you would normally expect the 3300ppm tempco resistor in similar circuits.
This leads to an eady way to check whether a tuning problem is related to the photocoupler circuit at all: measure the voltage on pin 7 of IC18. Within regulation it should be somewhat between -2 and -6 volts, -3 are more normal.
When the loop breaks open due to failure of the photocoupler or related parts, it will be stuck on the maximum negative output, something around -13 volts. There must always be a small current through the LED, otherwise the loop does not work and the TUNE HIGH preset has no effect!
Fact 2: the types VTL5C2 and VTL5C3 which are widely discussed as replacments are simply the wrong choice. In order to make the regulation work, the LDR resistance needs to be in the range of below one to a few kiloohms. The maximum LED current is limited by design to slightly over 2 mA. According to the datasheet, a VTL5C2 has 2 kiloohms at 2mA – regulation will never take place! Even if it seems to work, the controller will work close to the margin and operation cannot be guaranteed. Furthermore, resistance variation is quite large for those devices; the VTL5C2 I have tested had about 20kohms at 1mA.
The diagram below shows a known good original part (blue graph) and a VTL5C9 (yellow graph, values from the datasheet)
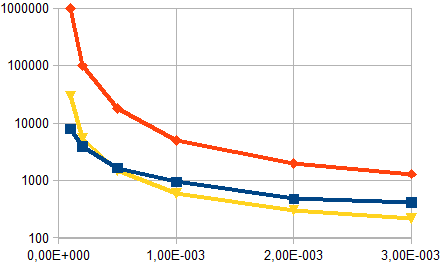
As you may have expected from my previous text, the red line represent the data sheet values for a VTL5C2.
While the VTL5C9 closely matches the original part in the most interesting region, the VTL5C2 resistance is way too high for any current.
What about RoHS…?
Photocouplers with LDRs are, as any LDRs which are commonly based on CdS (cadmium sulphide), forbidden for new products within the EU for some years now.
There is an exemption for the use in electronic music instruments, because there is no practical solution to control varying ac voltages better with LDRs.
(MOSFETs, for example, become highly nonlinear introducing distortion).
In this special case – a closed control loop and very small voltage variation across the device – a photo-mos device would probably be possible.
But it won’t be a solution for the control of audio signals in many applications. The EU has decided that science will have developed and indutry produces an alternative from december 31, 2013 on.
Science hasn’t, and industry doesn’t – except from Macron, who even try to force the EU to withdraw the exemption. Unfortunately, their devices are now way available at major european distributors by now…
Although it is always a good way to reduce hazardous substances, eurocracy has lost any sense of proportion for this topic. While power toys (sorry, I refuse to claim such crap tools) with short life spans flooding the market at low prices are allowed to contain batteries with large amounts of Cd, small photocouplers containg micrograms of Cd typically used in high-priced gear which will last for decades and serviced in case of a problem are to be banned.